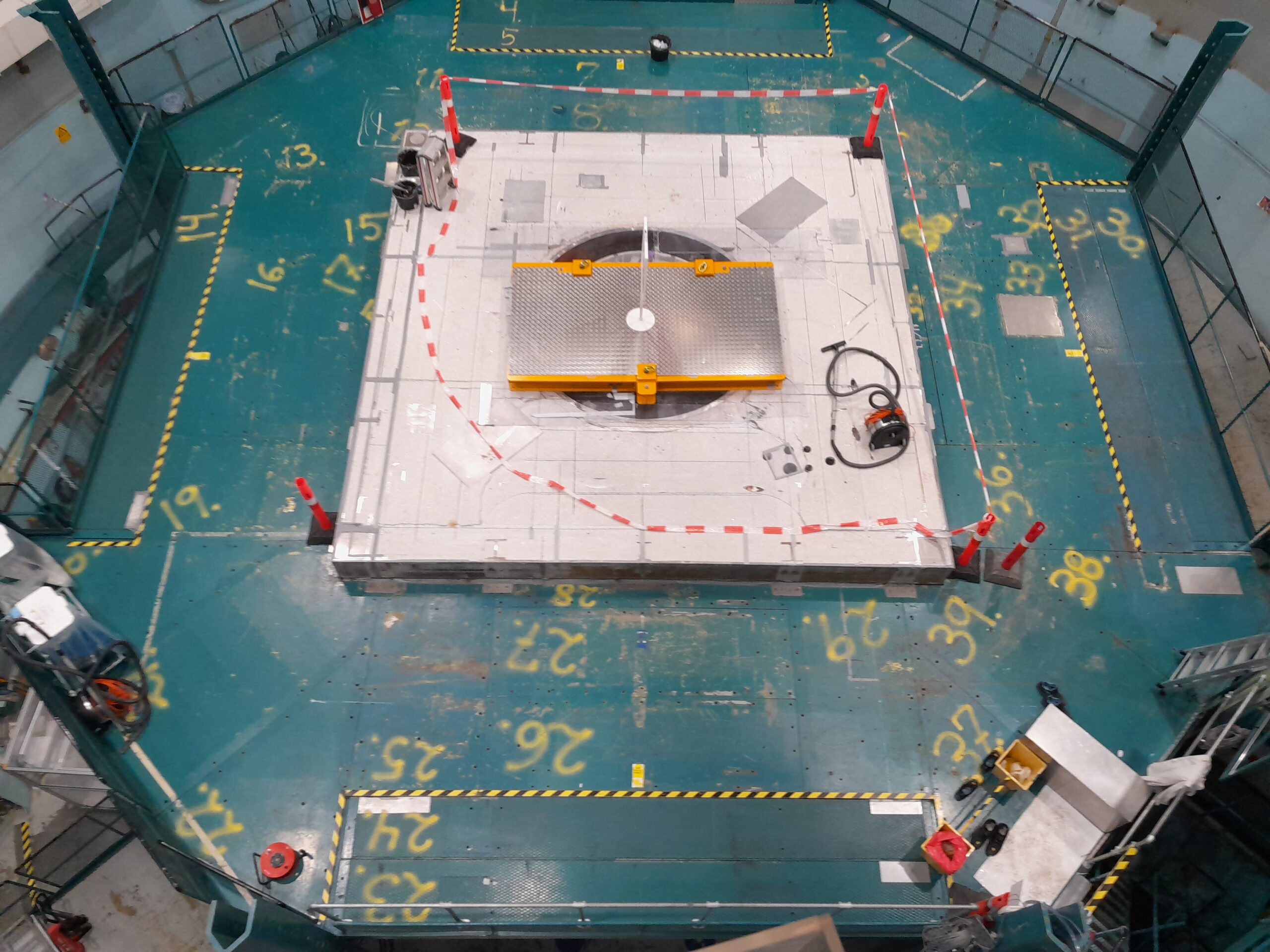
12 Jan Moving the working deck of DR3
In Danish Decommissioning there are ongoing tasks that are not found in many places and one of these is the relocation of the more than 60 years old working decks in the Danish Reactor 3 (DR3)
Working in a former research reactor is in itself a unique and in many ways special task, which makes unique and special demands.
Combine this unique working frame with a solid steel deck of more than 120 parts that must be disassembled, moved down and reassembled, and you have one of those jobs that doesn't exist in many places in the world.
Why the working deck is moved
Since 2021, Jonas Bie Mahler has been project manager for the decommissioning of DR3, Denmark's largest research reactor, both physically and in terms of energy.
A process that has been ongoing since the establishment of Danish Decommissioning 19 years ago, in 2003, and where among other things the relocation of the working deck is one of the many tasks involved.
Right now, the decommissioning of DR3 is at a stage where the concrete that has surrounded the reactor core, what is technically called the reactor block, is being cut. This block is made of concrete several metres thick, mixed with steel balls to increase its density and shielding against radioactive radiation, and cut into large pieces with saw blades.
It is a laborious process, and fundamental to this process is that the work must necessarily take place on a stable and durable surface, and this is where the working deck comes in.
A working deck that has been chosen to be maintained as it offers some obvious advantages in the work of decommissioning DR3.
"The deck of DR3 has been part of the design of the reactor from the start. So it was obvious for us to use it to work on, rather than having to tear it down, decommission it, and work with scaffolding," says Jonas Bie Mahler.
Now the decommissioning of DR3 has reached the stage where the working deck has to be moved further down in order to be able to saw more of the reactor block, but the move itself is also a time-consuming process.
How to move the working deck
To understand the dimensions and design of the work deck, you need to understand what the intention of the design was.
Jonas Bie Mahler says: "The deck is designed to hold our transport bottles, one of which weighs 23 tonnes and takes up about 1 square metre of floor space and is over 4 metres high. So it's a very heavily built deck, with some huge beams. Compared to what we use it for today, it's now really massively dimensioned, but it provides a lot of stability."
The working deck itself is built up of a kind of shelf brackets, which are mounted on the reactor block itself in a bracket with different levels. Solid steel beams are then placed on these shelf brackets and clamped to steel columns fixed to the floor. Finally, 39 plates are placed on top of the steel beams, which together form the surface on which work is going on above.
In itself, the operation is not necessarily terribly complicated, as long as you know the drawings and the method of proceeding, but it is cumbersome and time-consuming.
"To move the work deck, the shelf bracket must be removed and this requires everything to be disassembled. You can't partially lower the deck, or lower parts of the deck independently, but the whole thing has to come apart. And that takes space and it takes time." Explains Jonas Bie Mahler.
Challenges arise continuously
Rune Duelund Nielsen is one of the craftsmen who work daily in the former research reactor, and who is now helping to move the working deck for the second time in his time at Danish Decommissioning .
Rune Duelund Nielsen himself is one of the most important resources in the planning of the actual move of DR3, as he has previously been involved in moving it, and in addition to the drawings of the working deck, the practical experience and knowledge is extremely important.
Therefore, Rune Duelund Nielsen also knows the challenges that may arise during the process and how to meet them.
"The last time we moved the deck, we found that one of the big challenges we encountered was that they had chosen to paint the deck with some pretty heavy paint containing PCBs and lead. This had the effect that all the 'open' holes that the deck had to be moved down to and fixed into had threads painted over and the diameter of the holes changed. This meant that, at the time, we had to re-sand all the threads and holes to make things fit together. A grinding that of course also made some demands on work safety when working with PCB and lead."
In the same category of challenges, it was also discovered that as the working deck had not been moved for more than 40 years, there were some bolts and joints that had become very stuck and required creative solutions to free them.
Another impractical challenge in performing the task, and one that is inextricably linked to planning, is that the entire operation takes place in relatively confined spaces. For when the working deck is moved, the largest drop-off space in DR3 is also lost, and so creativity is required when the deck is dismantled and repositioned around the building. However, it is important that the parts are placed so that they are accessible when the working deck is rebuilt, so that you do not have to spend unnecessary time moving things around.
And in this context, the special ring crane plays a key role, but it is also one of the things that can bring challenges.
"Unfortunately, we have now experienced that the crane has required a repair in the process, and thus has not been able to run stably, so it puts the whole process at a standstill during the period when the crane is out of order, as it is essential to lift the work deck elements."
A final key issue that is always at the forefront of the move is work safety. This is not a challenge in itself, on the contrary, it is essential. But when you are working with such heavy elements and large machinery as is the case with the move, and at a height that requires securing, it obviously means that continuous adjustments must be made to ensure that safety is not compromised.
Things take time
The actual move of the working deck is estimated to take 4 effective working weeks, but as with all planning it's a trade-off of how quickly it can go if everything works optimally combined with a built-in buffer.
Looking ahead to the next time the deck will be moved or perhaps removed altogether, Jonas Bie Mahler does not expect another two years to pass.
"We have become significantly faster and much more efficient in the actual execution of cutting the reactor block. We have optimised on many points, for example by being able to run with two saws versus one saw previously, but we also hope to avoid external things like the Corona shutdown in the future."
In addition, he cites exhaust ventilation, larger cutting cages and experience with the equipment as contributing factors to the fact that today the work of cutting the reactor block is significantly faster than in the past.
At the same time, Jonas Bie Mahler knows that the further along in the overall process of decommissioning the entire DR3, the greater the complexity.
"It only gets harder the further along we get."
But for now, the focus is on moving the working deck of DR3 before Danish Decommissioning can start decommissioning Denmark's biggest research reactor again.